Connor Street: Made by Many Hands
2. Working in the ground
The following text is the second in a series by architect Kieran Hawkins, Director of Cairn, tracing the design and construction of an extension to a Victorian House in East London, recounting the everyday realities of the project and, in the green text, the broader environmental issues incumbent on architects to address. The texts have been developed by Kieran from a talk first given during the Poetic Pragmatism symposium, organised by David Grandorge and held at Waterloo City Farm on 25 March 2023.
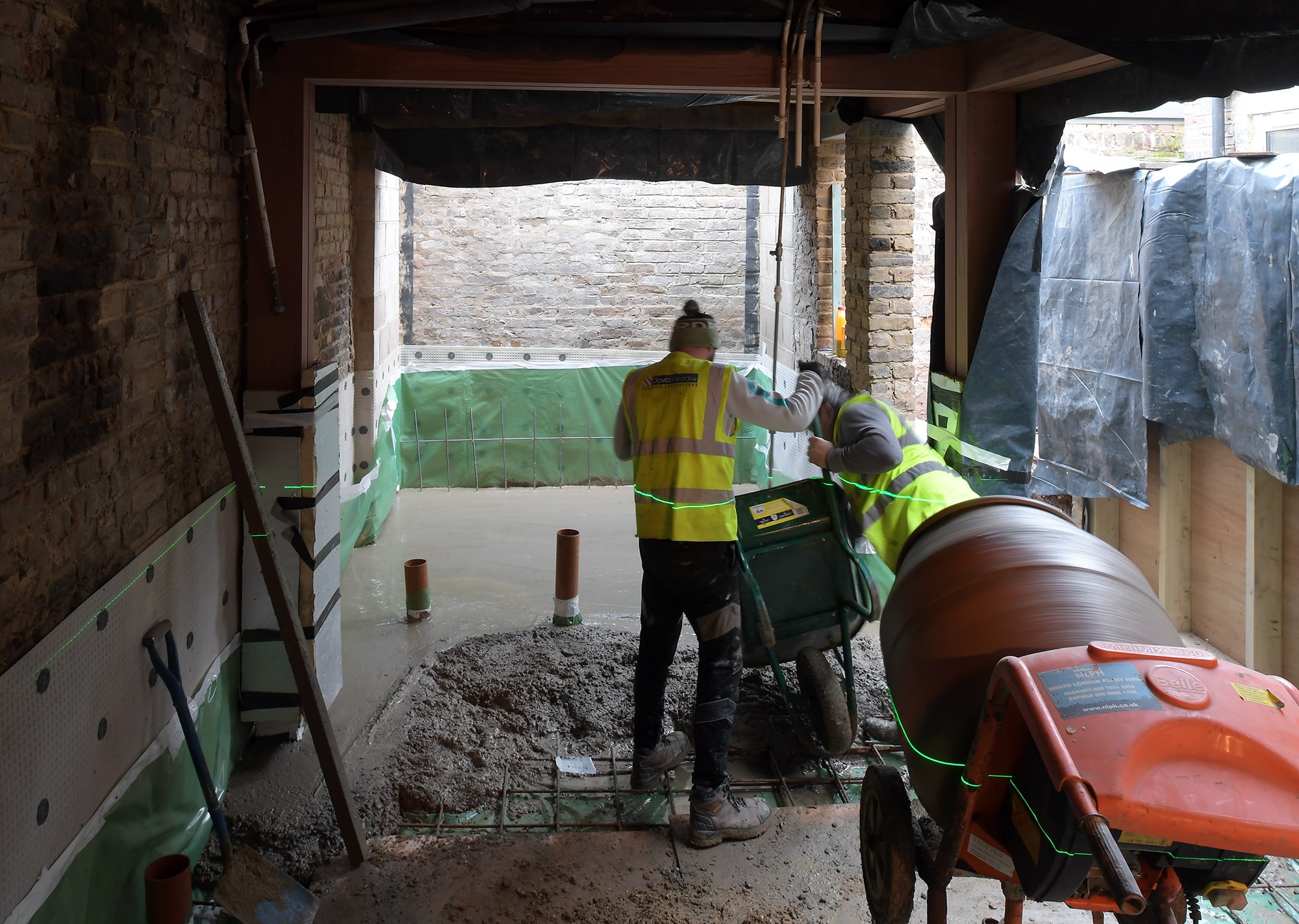
The Connor Street floor slab is the first building structure in the UK to use limestone calcined clay cement (LC3). This technology has been developed at EPF Lausanne, along with experts in Cuba and India, and generates 30-40% less CO2 than Ordinary Portland Cement in production. Structure Workshop were keen to use it here and publish the results. This is hopefully a significant step in the process of it being used more widely.
Our particular LC3 cement was sourced from an Italian manufacturer and shipped from Denmark. Delivery delays held things up slightly, but once on site it was very quick to install. When more widely adopted, and using local clays, UK merchants will stock this product and the shipping-miles can be wiped off the balance.
Importantly, concrete made with LC3 is mixed and poured in exactly the same way as that made with conventional cement, so no additional site training is needed. It was laid here by David Sheard and his team, an excellent contractor but not a specialist, as simply as all the many floor slabs they’d made before.
Cube tests were provided to Structure Workshop, who had done the research to source and specify LC3, despite it being little known in a UK context. The required C30 strength was achieved. Using these uncommon materials called for careful testing, which at times caught the team out. All targeted standards were reached, but on some occasions we got our results after the fact of the work. Not the calmest way to proceed, but good learning for our future use of non-standard materials.
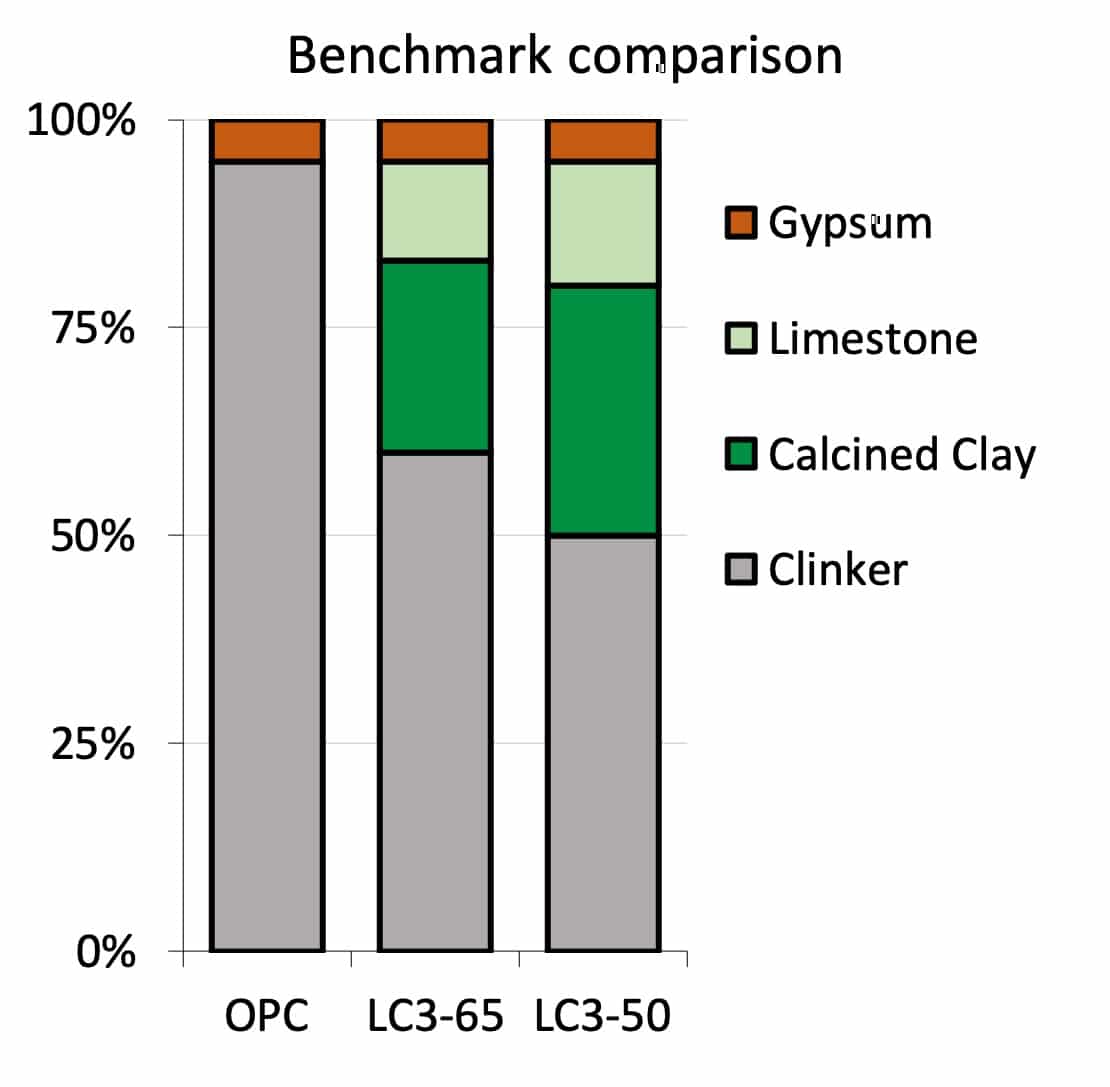
Many people I have spoken to are understandably sceptical about any use of concrete whatsoever. They reject adaptations to make it less damaging to the environment, taking the position that this will serve to falsely ease consciences and might slow transitions away from the material.
I respect their certainty and I am myself torn. Concrete is said to be the second most used substance on earth, after water. The concrete industry accounts for approximately 7% of all global carbon emissions. And the damage caused by our enormous reliance is far greater than that caused by these emissions alone, with the extraction of vast quantities of sand a particularly acute issue.
It will continue to be used on a huge scale in the medium term at least, especially in the Global South where there will be enormous urban and infrastructural expansion in coming decades. To meet the explosion in the urban population, an area of city equivalent to one new Paris will be built every week between now and 2050. More than half of worldwide concrete production is in China alone.
I hope there will be a breakthrough in materials to take its place; in the meantime, it is essential to make concrete less harmful. Large-scale systemic change is needed, but it won’t be an overnight revolution. Incremental steps are vital alongside this. LC3 could have a big part to play. If all Ordinary Portland Cement was swapped for LC3 tomorrow, global CO2 emissions would reduce by 2-3% overnight.
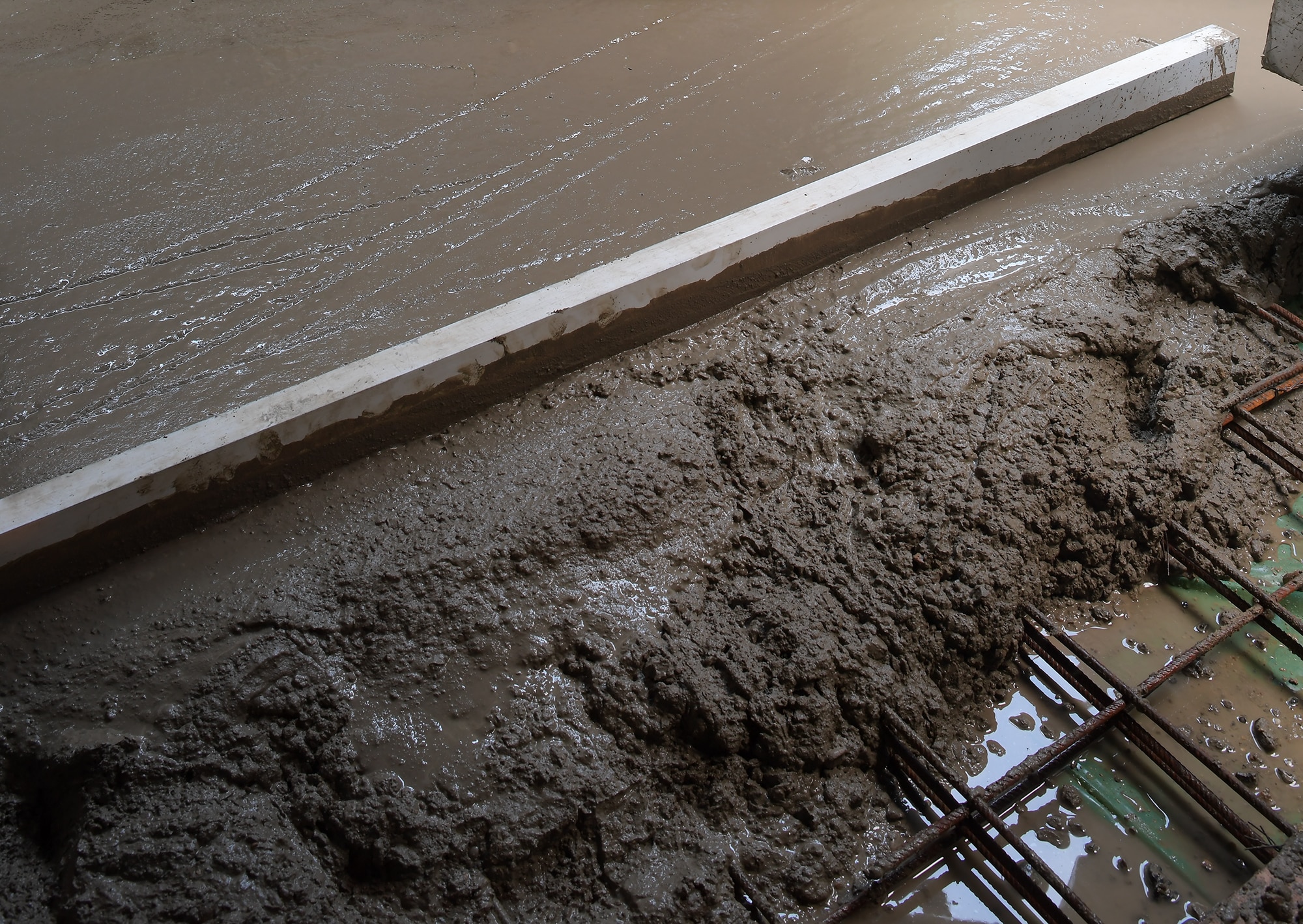
Several trial pits had been dug before work started, to ascertain the depth of existing footings and soil conditions. The particular conditions did not allow for a suspended timber floor or screw piles that would have reduced the concrete volume as much as possible, but the finished floor level was carefully set according to the findings to minimise requirements for underpinning.
Despite these tests, when excavation began in earnest much of the existing footings were revealed to be built on dusty weak-mix cement, falling away when touched like dry sand. The trial holes had been deceptively positive. Frustratingly, far more underpinning was required than we’d intended, with significant financial implications for the clients. There was at least some consolation for them that the concrete utilised the LC3, so the carbon cost didn’t sting quite as much as the blow to their bank account.
A key difference here to earlier projects was that we focussed more clearly on the design of the substructure at the start of the design, planning to minimise the depth and extent of new foundations and reducing any use of concrete. Site investigations and trial pits became a key input for the early design, even if they were revealed as misleading.
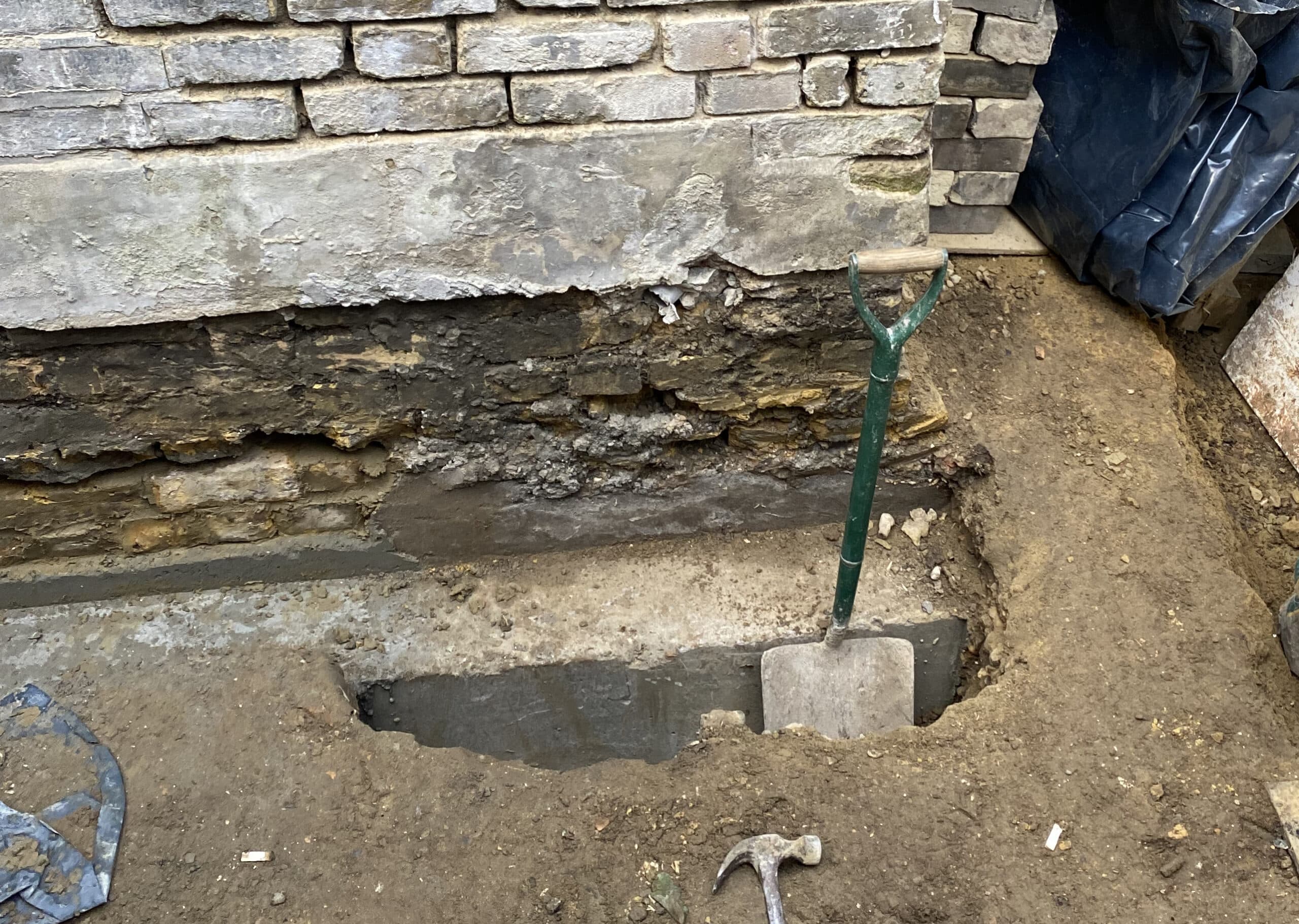
The low carbon concrete substructure was one of the most innovative aspects of the project and if it helps with the broader adoption of LC3 it may prove to be one of the most impactful specifications of my own career. It’s completely invisible and has no impact on the experience of the house.
As we combat climate change it will be the prosaic buildings that have the most impact. Multiple commonplace projects are more critical than a small number of remarkable exceptions. And it will likely be the hidden areas of these banal projects that have the biggest impact of all. If we can make low energy substructures and frames the standard practice in all our work to existing houses, the cumulative improvement will be huge.
Our approach allowed the project’s lifecycle embodied carbon to drop to approximately 40% of where it would have been if building with conventional materials. We worked closely with Structure Workshop to achieve this reduction and the emissions we conservatively calculated with them was 222 kgCO2e per sqm.
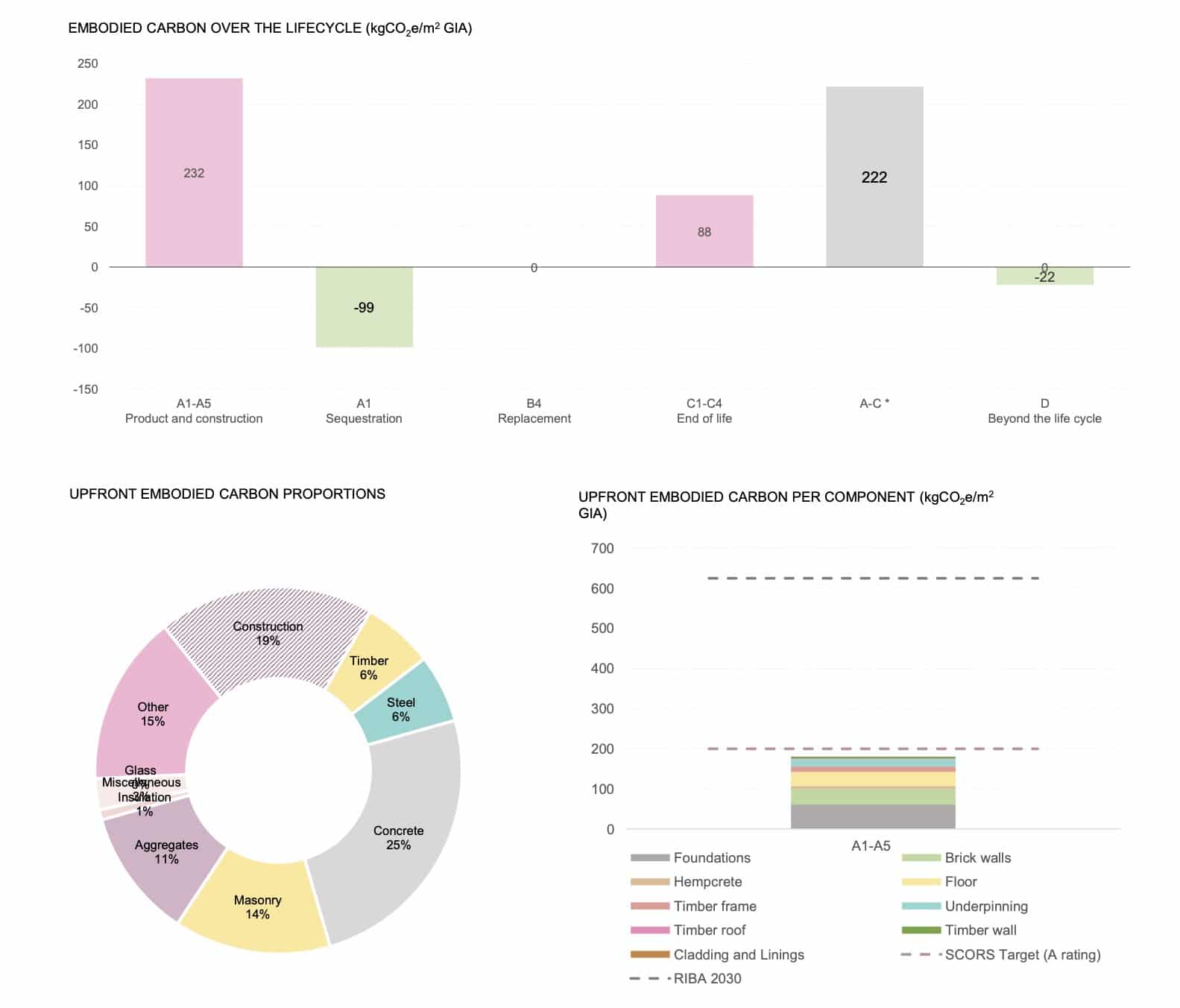
The Carbon Calculator developed by Structure Workshop was used to assess the carbon impact of material decisions.
While the embodied carbon figure is useful to make a point and to indicate a particular rigour, I am not certain how helpful it is for architects to focus on figures when making low energy buildings. Of course, it is valuable for aspects of our work to be quantifiable, to measure performance and verify claims, but I am not sure this is where architects’ energy is best focused. I am inclined to see our primary role in the de-carbonising of construction as providing the motive force, guiding conscience and a clarity of intent. To weave together calculations of specialists into some coherence while maintaining an emotional, experiential core to the work.